From Mattresses to Sunglasses: Turning CO2 Into Plastics
Meeting the obligations of the Paris Agreement is about more than 'just' cutting greenhouse gas emissions – it will also require actively removing carbon from the atmosphere and capturing it at points where emissions occur. Scaling up carbon capture technologies means finding economic value from captured carbon dioxide (CO2). One of the most promising applications of captured CO2 is in plastics manufacturing, as an alternative to feedstocks from fossil fuels.
From crude oil to captured carbon
Despite growing interest in alternative feedstocks, the vast majority of plastics are made from non-renewable fossil fuels. Most plastic begins as crude oil, which is taken to a distillation unit for separation into lighter components called fractions: mixtures of hydrocarbon chains. These chains are used to build polymers with various useful properties.
One of the most promising uses of captured CO2 is as an alternative feedstock for plastic manufacturing, replacing crude oil, natural gas, and coal. Although there are many approaches to turning CO2 into a polymer, they could all be loosely described as forms of artificial photosynthesis, in which energy is used to convert carbon dioxide into carbon-based products.
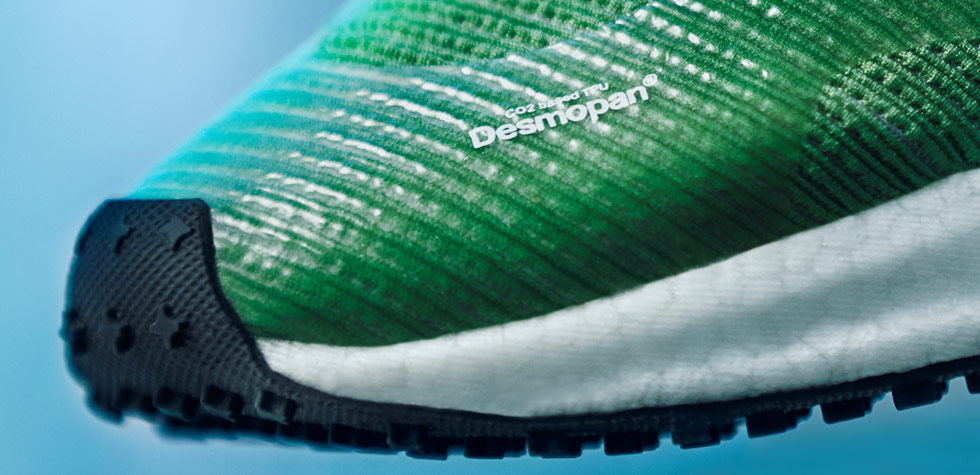
The amounts of energy necessary to transform CO2 – a very chemically stable molecule – would be vast and impractical if it were not for catalysts: materials that increase the rate of a chemical reaction. For this reason, most research on CO2-to-polymer conversion is focused on designing catalysts to make the transformation more efficient. Copper catalysts are particularly effective. For example, by reacting CO2 with water on the surface of a copper-based electrode, an oxygen atom is stripped from its molecules to create CO (carbon monoxide) which can then be turned into plastics and other products through subsequent reactions.
Commercializing CO2-based plastics
Several CO2-based polycarbonates – a family of thermoplastic polymers – are already commercially available, containing up to 50 percent CO2 by weight. For instance, German company Covestro AG joined forces with RWTH Aachen University to develop a catalyst for transforming CO2 into polymers. Their catalyst helps CO2 react with epoxy resins to form polyols (key building blocks for polyurethanes such as foams and binders) which contain up to 20 percent captured carbon. The company's Dormagen facility takes CO2 straight from the exhaust of a neighboring chemical plant as feedstock to make polyol for mattress foam, sports floor binders, and car interiors. With collaborators, the company is in the process of developing rigid insulating foam and synthetic fibers for garments.
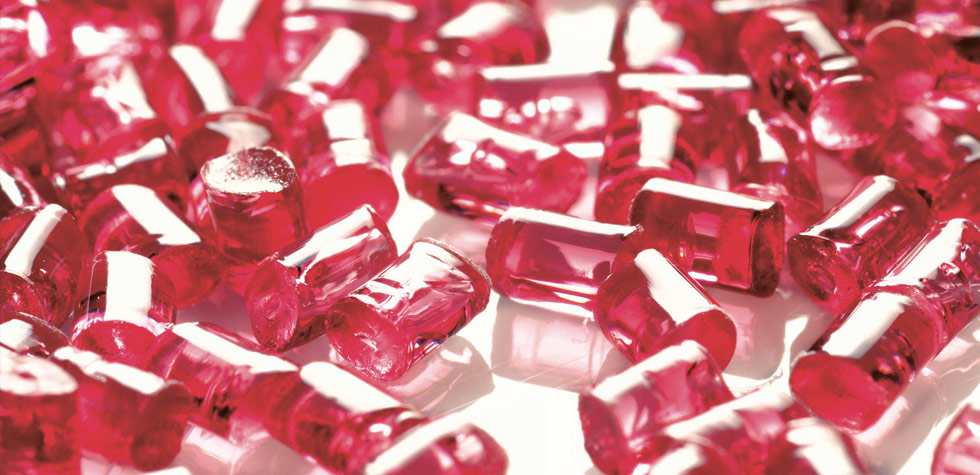
UK-based Econic, which is also producing polyurethanes from CO2 via polyols, told the BBC that CO2 is so inexpensive at $100 per metric ton (the standard raw material, propylene oxide, costs around $2,000 per metric ton) that a plant with a 50,000-tonne annual output could save $10 million per year by switching to captured carbon feedstock.
Research efforts are underway to refine countless new ways of incorporating CO2 into polymers. At the University of Sheffield in the UK, researchers have demonstrated turning CO2 – mainly from hydrogen production – into polyacrylamide: a polymer with a very wide range of applications. Scientists at Swansea University are working to develop copper catalysts to transform CO2 into ethylene: the core component of polyethylene. Berlin-based Made of Air, meanwhile, has developed a carbon-negative material which stores two metric tons of CO2 equivalent for every metric ton of plastic. The bioplastic, made from carbon sequestered in farm and forest waste, has been used in products including limited edition sunglasses for clothing manufacturer H&M.
A market for captured carbon
Many of these applications aim to manufacture plastics that will remain stable and last a lifetime, such as in construction, consumer products, and automotive parts. While some applications of captured carbon end with CO2 released to the atmosphere (such as in enhanced oil recovery), these applications trap carbon – serving as both carbon utilization and storage.
The technology to capture carbon already exists, both at emission sources and from the atmosphere, as do some processes for incorporating CO2 as feedstock into plastics and other products. For these technologies to contribute net-zero emissions targets by trapping billions of tonnes of carbon that would otherwise contribute to climate destruction, it is necessary to provide economic impetus for their adoption. Switching to replacing some fossil fuel feedstock with captured CO2 would not only reduce demand for petroleum – it could also play an important role in building this market for captured carbon.